SAP functionalities
SAP functionalities - a benefit for quality management
It is often only tiny details that determine the quality of a series part. In hardly any other area of the economy is it more important than in production that the individual components meet the required standards. A tire with a certain rubber compound, an electronic sensor with a certain measuring accuracy or a screw with the right tensile strength: many stages of sampling are usually carried out before a product is ready for series production. As these test procedures are no longer recorded by hand on documents, companies' IT departments are also facing new challenges. QM processes are increasingly being digitalized with the help of suitable CAQ systems. It is therefore not only necessary to map these sampling processes as efficiently as possible in order to reduce costs in development, because a well-functioning quality management system has a major role to play. influence on the entire company.
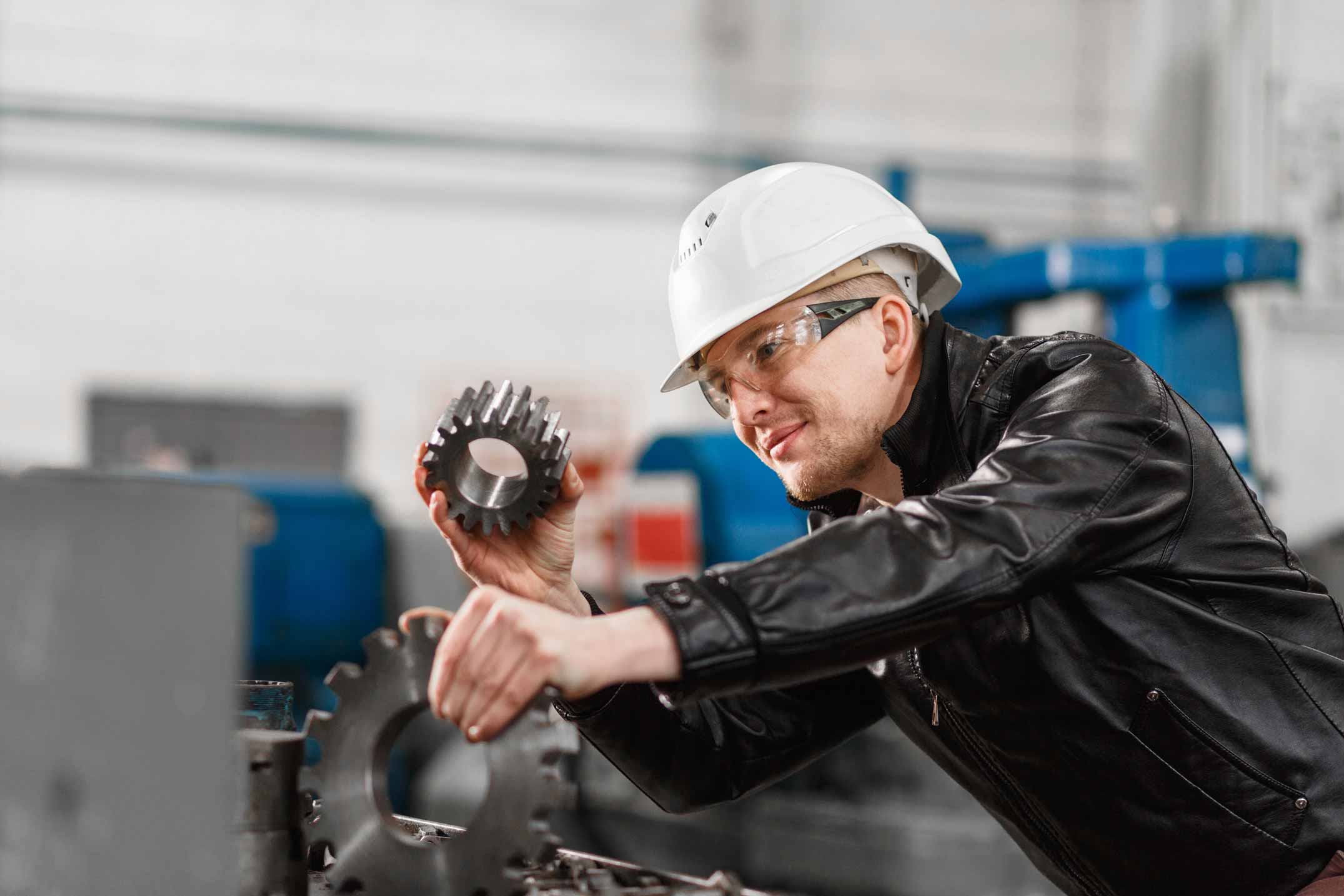
Quality management is fundamentally important for the company's success
Proof of high product quality is the basic prerequisite for achieving optimum customer satisfaction. The depth to which quality management can be optimized in every area of a company also brings with it a number of challenges. All production companies have always been under a great deal of pressure to innovate in
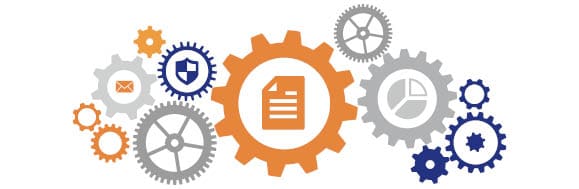
increasing price pressure. Quality standards must therefore be maintained and continuously improved with fewer financial resources. Although this trade-off is very difficult to map from a business perspective, there is no alternative to meeting existing quality requirements in order to avoid expensive recalls and consolidate the company's status as a reliable manufacturer. If an ERP is already in use, it is therefore advisable to first take a look at its QM functional scope before purchasing a separate CAQ system.
Quality management in ERP
Many successful companies rely on professional ERP software, such as SAP, in which all business-critical processes are mapped holistically. However, many company processes, including those in quality management, are not yet connected to the leading SAP system and, contrary to the growing digitalization, are still handled in the traditional way. This is surprising, as SAP already provides some basic functions for quality management "out of the box". In addition, functions that the standard system does not offer can be programmed more cost-effectively in the SAP system than if expensive license costs had to be invested in third-party software. However, there are some functions that can already be implemented very well with "standard means":
From the field: Workflow-supported sampling processes with CLC-PADD® PPAP+
Learn more8D Report
"An 8D report is a document that is exchanged between a supplier and the customer as part of a complaint, but it also functions as an internal document. 8D stands for the eight standard process steps that are required when processing a complaint in order to solve the underlying problem."
In the course of preparing an 8D report, the type of complaint, responsibilities and subsequent measures to rectify the defect are also defined. The 8D report is primarily standardized by the German Association of the Automotive Industry and is therefore particularly common in this sector.
SAP already provides a notification type in the standard system that is designed to map the 8D report. Interfaces to customer and supplier systems can be developed using the enhancement options for the QM report.
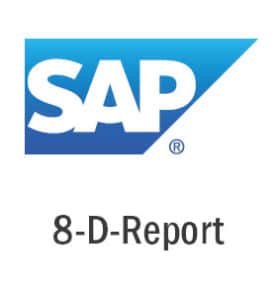
Automatic receipt of quality notifications
The automatic receipt of quality notifications: Customer complaints, notifications of defects to a supplier and internal notifications of problems can be automatically mapped in the SAP system. In these quality notifications, the problem description, the affected reference object (e.g. material), partner data, defect items and their causes can be defined. This allows these notifications to be displayed and processed in a very simplified manner. Automatic receipt and communication with the supplier (e.g. via EDI) can save costs very quickly and create transparency for the entire process.
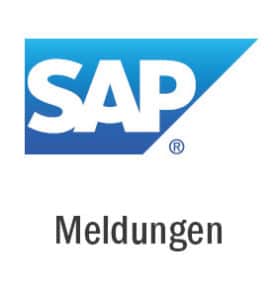
APQP
APQP: APQP loosely translated from English means "Advanced Product Quality Planning and Control Plan" (Advanced APQP Product Quality Planning). This is a very in-depth and complex approach to advance quality planning, meaning that it is more of a process than a single task. APQP covers all the steps to be carried out for the goods to be produced before the start of production. The focus here is on high quality. Standardized methods such as FMEA, QFD and QM plan are also used for implementation. The result of advance product quality planning is the basis for creating QM plans. With the possibilities of the SAP Cloud Platform, comprehensive process handling with customers and suppliers can be realized.
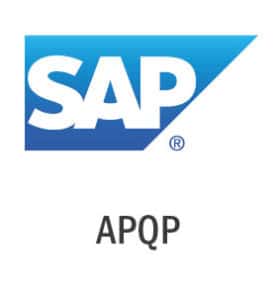
Sampling process
Efficient mapping of sampling processes in ERP: Sampling processes can also be efficiently mapped and controlled via SAP, even if SAP does not offer this function "out of the box". However, the PPAP or VDA2 standards as well as customer-specific standards can be easily mapped in the SAP system with "lean" additional functions.
Many systemic advantages can be achieved here within the sampling process. Quality reports (e.g. about defects or faults in products) are imported into the SAP system via various channels and can therefore be traced transparently. SAP integration also considerably simplifies the entire sampling process due to the necessary link with master and transaction data, such as the material master and parts lists, orders and inspection plans/inspection lots and goods receipt. The simple storage of the sampling documentation with a direct link to the relevant master data ensures that the documents can be found quickly and therefore saves an enormous amount of time. As a result, internal process costs can be greatly reduced and sampling becomes more transparent for all parties.
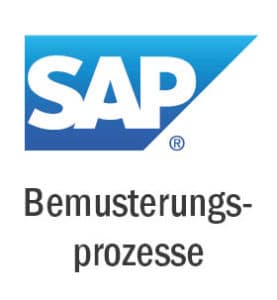
Discrete manufacturing is absolutely dependent on detailed mapping of samples
Particularly in discrete manufacturing, it is important to obtain the right and sufficient quality for each component in a targeted and precise manner. The in-house production process often demands extremely high quality standards, which makes sampling indispensable at this point. Depending on how many individual parts are on the bill of materials for the end product, sampling can be a significant time factor in the production process.
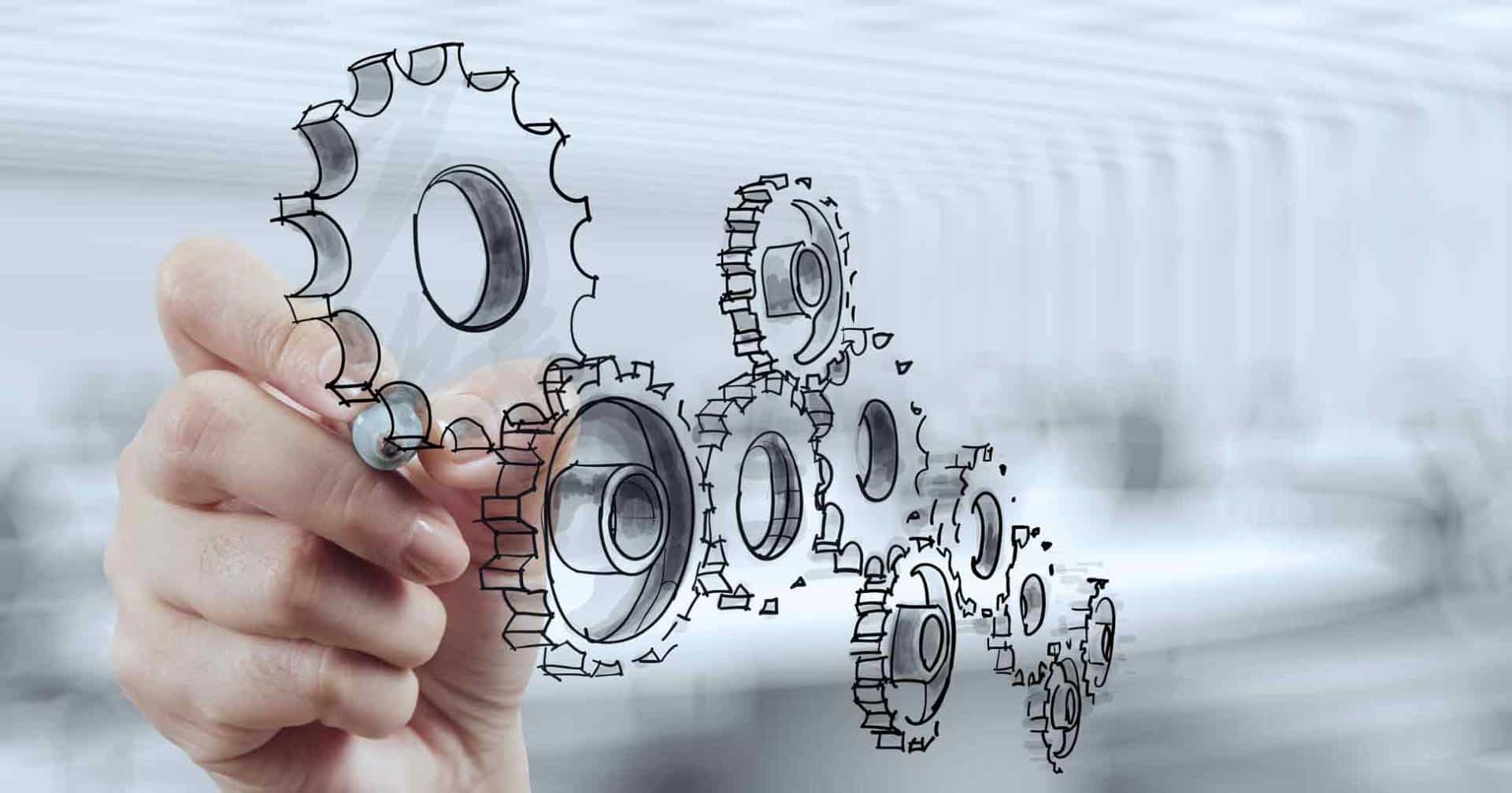
of the development. This is not a "choice", but of enormous importance to check and record the quality in detail during discrete production.
Each industry has different guidelines and requirements regarding suitable approval procedures. The PPAP (Production Part Approval Process), for example, is a production part approval process that is defined according to the AIAG (Automotive Industry Action Group) reference manual. PPAP sets out regulations that apply to the sampling process within the supply chain and to the series release of new parts. The aim of the process is to ensure regulated start-up assurance with regard to quality and quantity in series production. In the automotive sector in particular, this process can be mapped very well and efficiently in SAP, as CLC xinteg for example at their customer ZF Friedrichshafen AG successfully demonstrated.