CLC-PADD®
Efficient tool management in production
Those responsible for production and purchasing are often faced with the The challenge of not having reliable information about their tools at their disposal. Necessary information on location, condition, availability and interchangeable parts is missing or incomplete. This often results in a high level of uncertainty regarding model availability and a lack of cost transparency.
For companies that work with an SAP system, Implement a tool database without great effortwhich has the following advantages, among others:
Overview of all tools
Assignment and management of tools according to suppliers, locations and previously defined categories
Full transparency of repair data, costs, deadlines and documents for the individual tools
Reliable tool management for process owners
Overview of all technical specification features required for use in the production process
One in the SAP's integrated tool database enables an evaluation of the tool inventory, the repair overview and the usage overview. It also provides a solid basis for creating calculations and cost plans. By linking the tool master data with the movement data from logistics, it is possible, for example, to derive the number of shots based on the goods receipts and thus monitor the service life. If a tool is foreseeably no longer ready for use, a repair or scrapping and new procurement can be initiated at an early stage.
CLC-PADD® tool file - real added value
With the CLC-PADD® tool file, companies can benefit from the advantages mentioned above. The tool file enables the management of all relevant tool features and the storage of all tool documentation in a central location. As it is an SAP application, integration with standard functions from purchasing, logistics and production is extremely simple.
Flexible customizing allows you to adapt both the range of features and the folder structure for document storage to the specific requirements of your company.
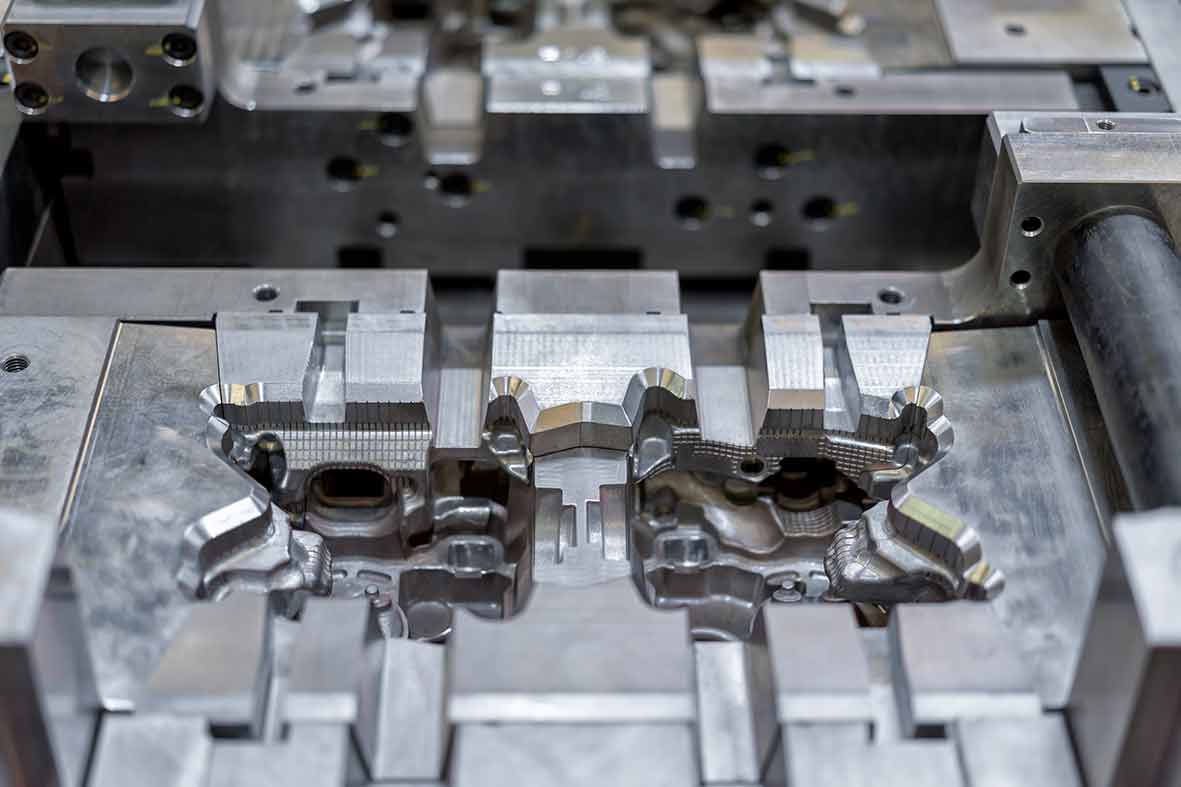